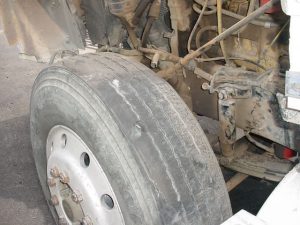
Photo our expert used to identify negligent maintenance issues even though trucking company had sold their dump truck out of state.
Tom was having a good day. Between sales calls, he stopped his pickup truck at a red light at the end of bridge waiting to turn left onto a freeway ramp. He had been sitting there about thirty seconds when he heard a loud screeching sound. A dump truck fully loaded with gravel crashed into his rear, crushing the bed of his pickup and knocking the top of his toolbox through his rear window. By the time Tom hired us, the dump truck company had sold the truck and “lost” all the maintenance records. However, we had an expert who could tell from photos of the property damage that there were rusty cracks in mechanical components that may have contributed to the crash. While driver distraction and speed were bigger parts of the case, proof of poor maintenance helped establish that the company had been sloppy about safety for a long time.
Although many of the commercial truck crash cases we handle are caused by some combination of speed, fatigue or distraction, some also involve mechanical failure. That may be discovered by a motor carrier enforcement inspection after a crash, in an expert inspection we arrange if we are hired quickly enough, or it may be disclosed later in expert examination of photos of property damage.
When mechanical problems are found after a crash, most often the root cause is in the company’s systemic failure to follow the well-established rules in maintenance management. Perhaps just as important, evidence of poor maintenance over a long period of time helps jurors believe that the company neglected everything else about safety.
Federal Regulations require trucking companies and key personnel involved with vehicle inspection and maintenance to understand and comply with rules on vehicle safety. The Federal Motor Carrier Safety Regulations at 49 C.F.R. § 396.1 mandates:
“Every motor carrier, its officers, drivers, agents, representatives, and employees directly concerned with the inspection or maintenance of motor vehicles shall comply and be conversant with the rules of this part.”
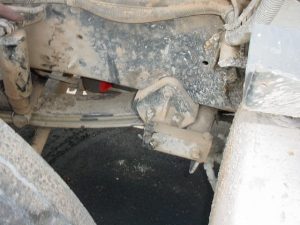
One of photos in which our expert pointed out evidence of negligent maintenance, even though trucking company had gotten rid of the truck before we were hired.
But too often when we dig out the truth behind a catastrophic truck crash, we learn that truck maintenance personnel were not trained and did not adequately understand what is required.
Regarding brake system, for example, the Federal Motor Carrier Safety Regulations at 49 C.F.R. § 396.25 outlines the following requirements for anyone who performs maintenance, inspection or repairs on air brake systems:
(a) The motor carrier shall ensure that all inspections, maintenance, repairs or service to the brakes of its commercial motor vehicles, are performed in compliance with the requirements of this section.
(b) For purposes of this section, “brake inspector” means any employee of a motor carrier who is responsible for ensuring all brake inspections, maintenance, service, or repairs to any commercial motor vehicle, subject to the motor carrier’s control, meet the applicable Federal standards.
(c) No motor carrier shall require or permit any employee who does not meet the minimum brake inspector qualifications of §396.25(d) to be responsible for the inspection, maintenance, service or repairs of any brakes on its commercial motor vehicles.
(d) The motor carrier shall ensure that each brake inspector is qualified as follows:
(d)(1) Understands the brake service or inspection task to be accomplished and can perform that task; and
(d)(2) Is knowledgeable of and has mastered the methods, procedures, tools and equipment used when performing an assigned brake service or inspection task; and
(d)(3) Is capable of performing the assigned brake service or inspection by reason of experience, training or both as follows:
(d)(3)(i) Has successfully completed an apprenticeship program sponsored by a State, a Canadian Province, a Federal agency or a labor union, or a training program approved by a State, Provincial or Federal agency, or has a certificate from a State or Canadian Province which qualifies the person to perform the assigned brake service or inspection task (including passage of Commercial Driver’s License air brake tests in the case of a brake inspection); or
(d)(3)(ii) Has brake related training or experience or a combination thereof totaling at least one year. Such training or experience may consist of:
(d)(3)(ii)(A) Participation in a training program sponsored by a brake or vehicle manufacturer or similar commercial training program designed to train students in brake maintenance or inspection similar to the assigned brake service or inspection tasks; or
(d)(3)(ii)(B) Experience performing brake maintenance or inspection similar to the assigned brake service or inspection task in a motor carrier maintenance program; or
(d)(3)(ii)(C) Experience performing brake maintenance or inspection similar to the assigned brake service or inspection task at a commercial garage, fleet leasing company, or similar facility.
(e) No motor carrier shall employ any person as a brake inspector unless the evidence of the inspector’s qualifications, required under this section is maintained by the motor carrier at its principal place of business, or at the location at which the brake inspector is employed. The evidence must be maintained for the period during which the brake inspector is employed in that capacity and for one year thereafter. However, motor carriers do not have to maintain evidence of qualifications to inspect air brake systems for such inspections performed by persons who have passed the air brake knowledge and skills test for a Commercial Driver’s License.
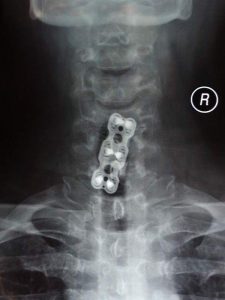
Tom’s neck after surgery required when negligently maintained dump truck crushed the rear of his pickup
But when a truck crash is caused, in whole or in part, by brake failure, we usually find that the person responsible for maintenance at the trucking company had no idea what a certified brake was, much less qualifying as one.
In addition, 49 C.F.R. § 396.13 requires:
“Before driving a motor vehicle, the driver shall:
(a) Be satisfied that the motor vehicle is in safe operating condition;
(b) Review the last driver vehicle inspection report; and
(c) Sign the report, only if defects or deficiencies were noted by the driver who prepared the report, to acknowledge that the driver has reviewed it and that there is a certification that the required repairs have been performed. The signature requirement does not apply to listed defects on a towed unit which is no longer part of the vehicle combination.”
However, when mechanical failure contributes to the cause of a truck crash, we are likely to find in depositions of the maintenance supervisor and the truck driver that the driver vehicle inspection report was never shown to any driver, either the driver that filled out the report or the next driver.
Another section of the Federal Motor Carrier Safety Regulations, 49 C.F.R. § 396.11, states:
“(c) Corrective action. Prior to requiring or permitting a driver to operate a vehicle, every motor carrier or its agent shall repair any defect or deficiency listed on the driver vehicle inspection report which would be likely to affect the safety of operation of the vehicle.Every motor carrier or its agent shall certify on the original driver vehicle inspection report which lists any defect or deficiency that the defect or deficiency has been repaired or that repair is unnecessary before the vehicle is operated again.”
When we dig into the records, we are likely to find the company did not comply with this rule either.
Requirements for annual truck inspections are outlined in 49 C.F.R. § 396, Appendix G. However, it is not unusual to find that the person in charge of maintenance was unfamiliar with this requirement, and therefore could not credibly sign off on inspection requirements with which he is unfamiliar.
That very knowledge on the part of maintenance personnel is required of trucking companies. The Federal Motor Carrier Safety Regulations at 49 C.F.R. § 396.19 requires:
“(a) It shall be the motor carrier’s responsibility to ensure that the individual(s) performing an annual inspection under §396.17(d) (e) or is qualified as follows:
(a)(1) Understands the inspection criteria set forth in 49 CFR Part 393 and Appendix G of this subchapter and can identify defective components;
(a)(2) Is knowledgeable of and has mastered the methods, procedures, tools and equipment used when performing an inspection; and
(a)(3) Is capable of performing an inspection by reason of experience, training, or both as follows:
(a)(3)(i) Successfully completed a State or Federal sponsored training program or has a certificate from a State or Canadian Province which qualifies the person to perform commercial motor vehicle safety inspections, or
(a)(3)(ii) Have a combination of training and/or experience totaling at least 1 year. Such training and/or experience may consist of:
(a)(3)(ii)(A) Participation in a truck manufacturer sponsored training program or similar commercial training program designed to train students in truck operation and maintenance;
(a)(3)(ii)(B) Experience as a mechanic or inspector in a motor carrier maintenance program;
(a)(3)(ii)(C) Experience as a mechanic or inspector in truck maintenance at a commercial garage, fleet leasing company, or similar facility; or
(a)(3)(ii)(D) Experience as a commercial vehicle inspector for a State, Provincial or Federal Government.
(b) Evidence of that individual’s qualifications under this section shall be retained by the motor carrier for the period during which that individual is performing annual motor vehicle inspections for the motor carrier, and for one year thereafter. However, motor carriers do not have to maintain documentation of inspector qualifications for those inspections performed either as part of a State periodic inspection program or at the roadside as part of a random roadside inspection program.”
The Federal Motor Carrier Safety Regulations at 49 C.F.R. § 396.25 requires that the brake inspector must be “knowledgeable of and has mastered the methods, procedures, tools and equipment used when performing an assigned brake service or inspection task.” But when brakes fail, we are likely to find that the maintenance personnel lacked the knowledge of how to deal with a simple brake out of adjustment with an automatic slack adjuster, which disqualifies them as brake inspectors.
When there is a truck crash in which mechanical problems are an issue, when we review personnel files of trucking company mechanics, we are likely to find that they too are deficient in training, experience or certification.
While we seldom see a truck crash case in which mechanical failure is the sole cause, if hired early enough we are able to get a thorough inspection to find what mechanical issues are involved. In representing the victims of a catastrophic truck crash in which mechanical issues are involves, we work closely with experts who inspect the truck and guide us through the technical details required to build the case.
——–
Ken Shigley is an Atlanta-based trucking, personal injury and wrongful death trial attorney. He is past president of the State Bar of Georgia, past chair of the American Association for Justice Motor Vehicle Collision, Highway and Premises Liability Section, past board member of the AAJ Trucking Litigation Group, and a member of the board of governors of the Academy of Truck Accident Attorneys. He is also lead author of Georgia Law of Torts: Trial Preparation and Practice and a chapter author of Handling Motor Accident Cases, both published by Thomson Reuters, and one of just eighteen Georgia lawyers who have earned double board certification in Civil Trial Advocacy and Civil Pretrial Advocacy from the National Board of Legal Specialty Certification. He may be contacted at ken.shigley@johnsonward.com or 404-253-7862.